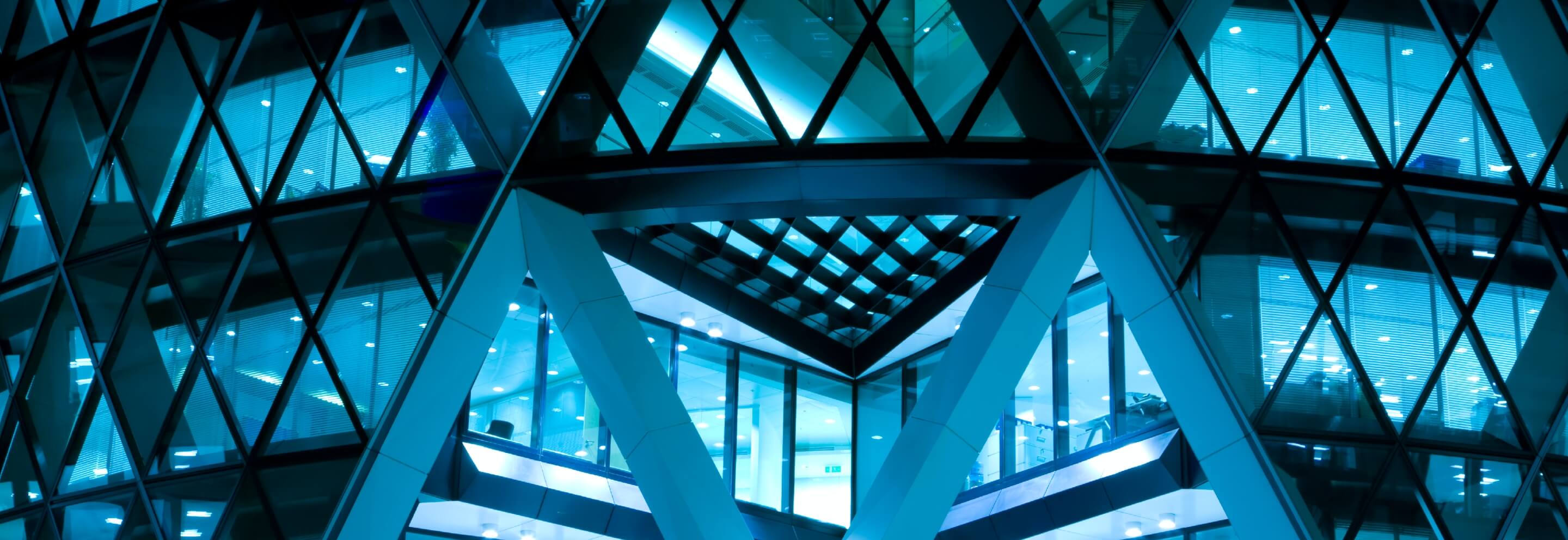
Blog
- Jun 27, 2025
- Cody Lirette
-
- Jun 25, 2025
- Meghana Joshi
-
- Jun 12, 2025
- Denis Cody
-
- May 09, 2025
- Cody Lirette
-
- May 05, 2025
- Cody Lirette
-
- Apr 11, 2025
- Cody Lirette
-
- Dec 23, 2024
- Lina Paerez
-
- Sep 26, 2024
- Christian Allred
-
- Jul 05, 2024
- Cody Lirette
-
- Jul 02, 2024
- Cody Lirette
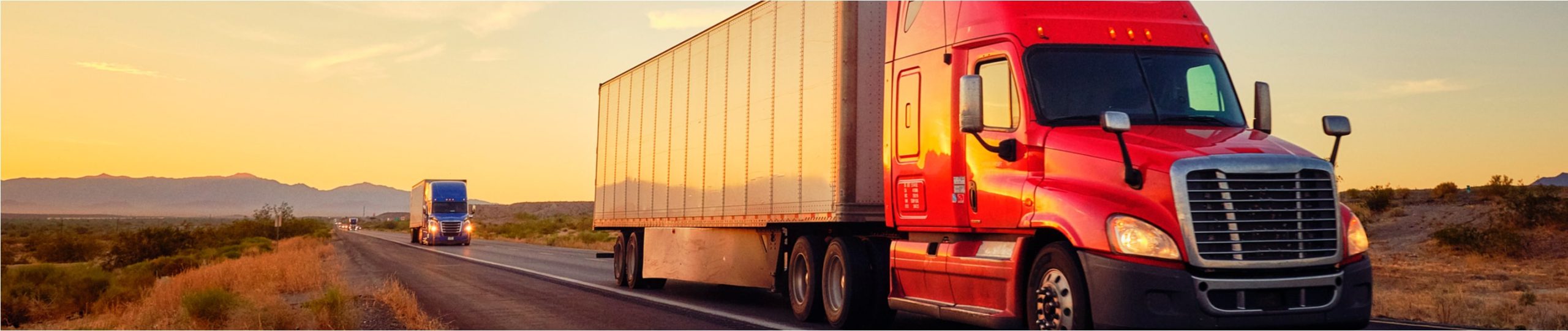
Digitalization is transforming industrial operations around the globe. Learn how ORBCOMM solutions can optimize yours.
Get a Tailored Quote