Container Operator Stays a Step Ahead with IoT Reefer Monitoring
- Blog
- Container Shipping
- Container Operator Stays a Step Ahead with IoT Reefer Monitoring
Discover how container services provider Balticon uses IoT reefer monitoring to improve asset visibility, control and customer service to some of the world’s largest shipping lines…
Polish company Balticon S.A is a container services provider and trader serving an international and domestic client base. With its main offices in the Polish seaports of Gdansk and Gdynia, plus depots and branches across Poland and beyond, the private company has built its annual turnover to approximately €20 million. Refrigerated container services are a core competency and make up around 40% of the business today.
In the international arena, Balticon helps container shipping lines, leasing companies and forwarders with their container operations in Poland and the wider EU market, providing storage and M&R services from its depot network, plus road and rail transport to and from Poland’s ports and the hinterland. The company operates its own fleet of tractors, chassis and gensets for dry and refrigerated container transport, with clients including APL, COSCO/China Shipping, CMA-CGM, OOCL, Hyundai Merchant Marine, Maersk Line, Textainer, Touax and Yang Ming Line.
In the domestic market, Balticon sells, leases and modifies dry and refrigerated containers as storage units and for use within manufacturing operations, as well as for transport operations. It has supplied reefer containers under the “Eco Cold Store” brand for use in a wide variety of industry sectors, including bakery, chemical, dairy, fish processing, flower trade, fruit and vegetables, medical and tobacco, among others.
The Challenge
In 2013, Balticon made its first steps into Internet of Things (IoT) connected assets, acquiring a first batch of ReeferConnect IoT reefer monitoring devices from ORBCOMM to test in its domestic rental operations. Using GPS and GSM technology, the IoT devices allow users to remotely locate and view the operating status of their refrigerated containers, with 2-way communications including remote temperature control, diagnostics and software updates, plus automated alarms.
Balticon’s rental clients receive 24/7 IoT reefer monitoring and maintenance, including on-site technical inspections and call-outs, to ensure their containers are fully operational and functioning to the required level at all times. The company wanted to assess how the introduction of a telematics solution, including a cloud application for live monitoring, could add value both for Balticon’s clients in ensuring cargo safety and quality, and for Balticon itself in better control over its reefer assets, plus improved customer service.
The benefits were swiftly validated, says Balticon CEO Tomasz Szmid. “We acquired the ability to remotely monitor and control our reefer units at clients’ premises all over the country. The system allowed us to know what’s going on at all times, both at the office and also with the chance to view real-time information on a tablet when out of office–and out of office hours. This allowed us to improve our speed of service and be proactive in ensuring that technicians are quickly dispatched as soon as a problem is detected, day or night.”
Szmid recalls the moment that the system really came into its own, when Balticon provided 44 IoT-connected reefer containers for a NATO training exercise in Poland. The containers were dropped way ‘off grid’ in deep forest to store food and other perishable supplies for the troops taking part. Thanks to the tracking technology, Balticon was able to maintain remote oversight of its equipment throughout the exercise. Luckily, no problems occurred with any of the reefer units but if they had, says Szmid, Balticon would have been alerted instantly and able to remotely adjust temperatures, or send personnel direct to the right location to carry out tests and repairs.
Some Balticon clients have very precise needs that require highly accurate refrigeration performance, adds Szmid. One such is a tobacco company currently renting 32 reefer containers, which it uses for pest eradication as an integral part of its production process. Tobacco leaves are stored inside the reefer containers, and the temperate is slowly reduced to -20°C over a two-week period. The temperature is then slowly increased back to ambient. This process kills off any pests in a natural way (similar to the cold treatment regime specified by the USDA for certain fruit shipments into the USA) without the need for chemical pesticides. Validating the accuracy of this process with hard data– and the ability to immediately detect any non-conformance– is crucial.
The Results and Next Steps
“It was very important for us that we were the first company in Poland to adopt this new technology, establishing us as a step ahead” says Szmid. Today, the system has become an integral part of Balticon’s operations. The company has so far equipped 120 of its existing 250 domestic rental reefer fleet with ORBCOMM telematics and is now getting ready to extend usage to the next stage. That includes an additional 20 x 40ft and 20 x 20ft new reefer containers currently being acquired to meet growing demand.
“With this technology, we can all sleep well,” says Szmid. “It has become the constant connection to our equipment.”
Download the full Balticon Case Study
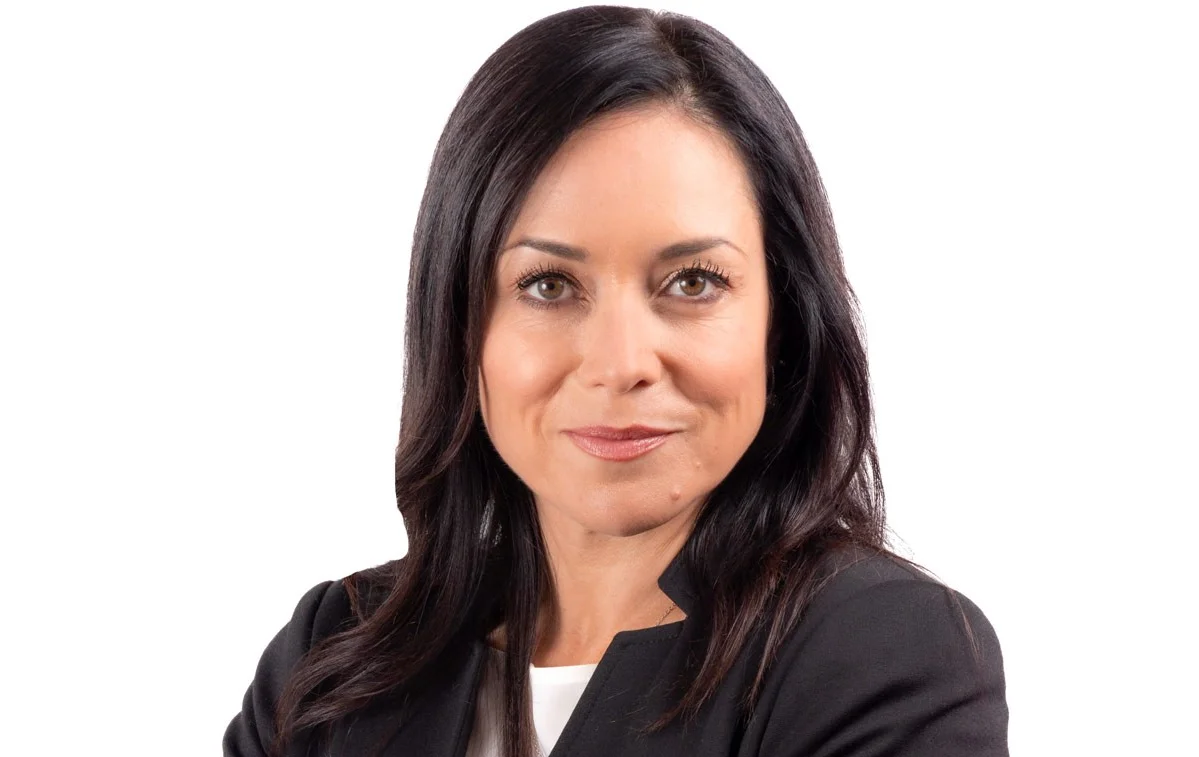
With over 15 years of marketing experience at companies big and small, Lina Paerez leads ORBCOMM’s global marketing team, driving key positioning strategies, product launches, demand generation and brand awareness.
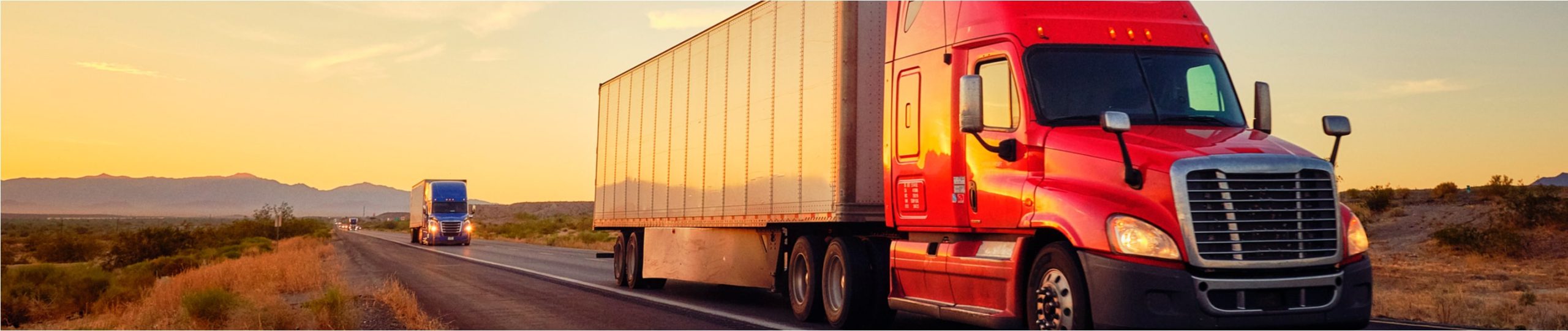