
How fleets can reduce rejected loads from broken door seals
- Blog
- Transportation
- How fleets can reduce rejected loads from broken door seals
- May 12, 2023
- Dean Gobrecht
Missing or broken door seals can hurt carriers and receivers alike. When a receiver discovers a broken or missing seal at delivery, they have the right to reject the entire load. This can be costly for carriers, as loads that have travelled for hundreds of miles can be rejected at the destination without payment. Plus, receivers may lose sales or incur manufacturing delays due to rejected inventory.
Worst of all, according to many, this happens more often than one would think. Freight brokers are seeing consignees rejecting cargo when carriers show up at the delivery dock with broken seals. In both truckload and less-than-truckload shipments, shippers require their freight to be transported in “sealed” containers so that chain of custody can be verified.
In these situations, without any evidence of how a door seal was broken, it can be difficult to determine if a shipment has been tampered with, resulting in scenarios where loads are rejected despite the cargo being undamaged. To prove the integrity of cargo throughout their journey, trucking companies are turning to telematics technology.
What are door seals?
An essential part of cargo transportation, door seals are used in trailers to ensure the integrity of cargo. Ideally, once a trailer is ready to be shipped, the door seal is set and shouldn’t be broken until arrival—where the receiver can access their product. However, sometimes this doesn’t end up being the case.
How do door seals typically break?
Door seals can break for a variety of reasons. There are worrisome cases where a broken door seal can signify unauthorized trailer access and cargo theft or tampering, which would result in a rejected load. In this scenario, having visibility into what occurred within the trailer can prove valuable as it can reveal how it happened, helping carriers prevent further attempts on their cargo.
However, a broken door seal doesn’t necessarily mean cargo theft. It could be an oversight by the shipper where they write the seal number on the bill but forget to install it. Or it could be the driver broke the seal to investigate the cargo integrity after a road incident. Or it could be the result of a shipper adding cargo to the trailer to earn additional revenue.
These situations can still be frustrating for the receiver, but they often wouldn’t warrant load rejection unless the cargo is visibly damaged. However, without evidence, there’s no way of determining what caused a door seal to break.
Explain broken door seals with evidence
When a shipment arrives with a broken door seal and the load is being rejected, the best backup you can have is proof of how it happened.
Having documentation—such as driver statements, photographs and third-party inspections—can help build a case that the broken seal wasn’t due to tampering. Documenting these events when these happen and reviewing the findings can shine some light on frequent causes that can be preventable.
One of the most powerful tools for delivering concrete proof is through telematics technology. With end-to-end remote visibility through door sensors, geofencing and cargo camera sensor footage, shippers and their customers can understand the status of their cargo throughout its entire journey.
Telematics enables carriers to provide evidence of cargo integrity by verifying whether or not there was unauthorized trailer access. This can drive considerable ROI, as it can help eliminate instances where a broken door seal that wasn’t due to attempted cargo theft resulted in a rejected load.
Improve cargo security with ORBCOMM
A load can be rejected for a variety reasons, and a broken door seal is one of them. By providing more visibility around these events, shippers can reduce rejected loads, saving time, money and reputation.
Learn how our full suite of cargo security devices—including door sensors and cargo camera sensors—can deliver full remote trailer visibility to help validate cargo integrity and ensure shippers and receivers are aware of everything that happens to their cargo.
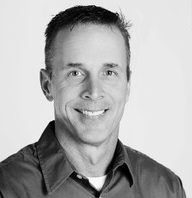
Dean Gobrecht is a Pre-Sales Engineer for the North American transportation industry. Using his vast technical knowledge of fleet management, transportation claims, telematics and analytics, Dean helps provide data-driven solution recommendations to ORBCOMM customers across the United States and Canada.
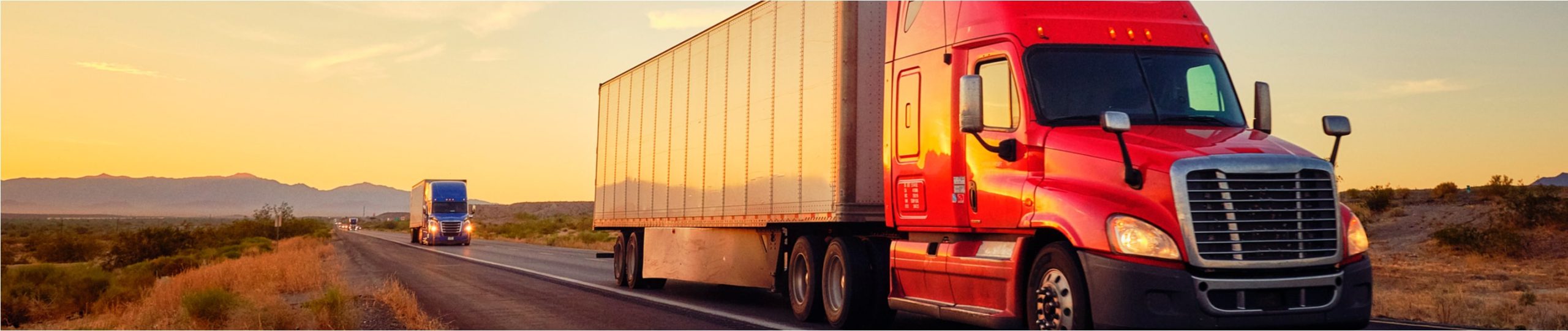